Precision Process designs, builds, and installs reel to reel plating equipment for the international market. We offer high-speed plating equipment in a variety of configurations with a multitude of optional cells for overall or selective plating.
Materials options include: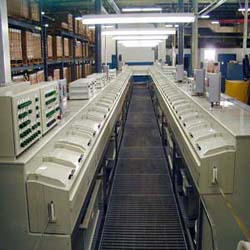
- Copper alloy strip and wire
- Bandoliered contacts
- End and center carried contacts
- Steel strip
- Copper and aluminum foils
- Mylar and other plastic strips
Configurations include:
- Single and multi-strand lines
- Straight and U shaped lines
- Horizontal or vertical transport
Finish options include:
- Copper (acid/cyanide)
- Nickel (woods, sulfamate, watts)
- Gold (soft, hard)
- Palladium and Palladium-nickel
- Tin (bright, matte)
- Tin-lead (various alloy compositions)
- Reflow of tin and tin/lead alloys
Processing options for plating cells
We use a wide variety of innovative cell designs in our reel to reel plating equipment, including Zero Discharge Rinse Systems, selective depth, multi-mode, bubbler, stripe, spot, and spray jet.
Zero Discharge Rinse System
Precision Process designed its Zero Discharge Rinse System to reduce water consumption at each rinse stage. By using the concept of triple counter flow rinsing in the lower reservoir, the system allows the amount of fresh incoming water to be balanced with evaporation losses occurring in the preceding chemical process cell (cleaning, plating, etc.). Each Zero Discharge Rinse System consists of a series of four rinses, including spray rinses, spray-under-immersion rinses, or a combination of the two. The final stage features an air atomizer, using a combination of air and water to provide a fine rinse mist with minimal water usage.
Selective depth
Whether the application is a simple alkaline soak cleaning, or controlled depth plating, the basic concept of the all-over type process cell is the same. We fabricate each cell from a suitable chemical-resistant material, such as polypropylene. An external reservoir feeds fresh solution into a false bottom in the process cell, via a transfer pump. A sparger plate in the cell allows solution to be rapidly and uniformly distributed throughout the cell. Solution overflows the sides of the cell into an outer containment trough, where it eventually drains back to the reservoir. Weir gates at each end of the cell minimize outflow where the strip enters and exits the cell. An air wipe at the exit minimizes dragout.
Applications:
- Soak clean
- Acid activate
- Immersion rinse
- Over-all plate
- Controlled depth plate
Stripe
Single and multiple stripe widths can be applied to strip product via stripe belt cells. These cells utilize both inert and soluble anode systems using both fabric backed belt or titanium belt materials. Various belt surface materials include soft and hard neoprene foam, PVC and RTV coatings. Typical stripe widths can be held to +/- .010” over cell distances from 87” to 106” in length. Stripe cell boxes are designed for ease of operator use with all controls available on the front of the units. Stripe head systems are designed for use with gold and tin – tin alloy chemistries.
Bubbler
Our bubbler cells are uniquely fabricated for plating internal recesses of female sockets and clips. The cell buss design allows switchover from center anode, outer anode or both when using this type of selective cell. The various available weir design arrangements in our selective bubbler cells overcome the many type of contact designs which prevent the ability to deposit adequate plating thickness inside connector sockets thus eliminating the problems.
Spot
Precision Process has the capability to deposit precious and non-precious metal plating deposits in the form of defined spots on a part or strip. The ability to reduce precious metal consumption is the reason more customers are adapting this technology over standard selective depth and stripe techniques. Our proprietary spot technology can be applied by two types of methods (belt or wheel) with typical spot placement of +/- .005” on location on repeatable progression. We can provide equipment to plate one side or both sides of a part and will work with your designers to suggest the most appropriate equipment to perform the job.
Spray Jet
The spray jet cell is used in applications for selectively plating stamped reel to reel parts and as an alternative for belt stripe equipment. The spray jet cell system delivers the plating bath chemicals from the plating tank through a high flow/high pressure manifold and into a faceplate machined to the contour of the part. The faceplate serves to fixture the parts through the cell and as a medium for directing the plating to the specific area of the part. The jet cell uses technology developed through years of testing in production applications. Equipment can be setup for single or dual stripes on one side of a part or both sides.
High Speed Over-all
Many reel to reel applications require high speed overall cells which allow for faster plating rates. This translates into higher line speeds. Precision Process has designed these cells for increased production capability in single or dual strand designs. Cell accessories include adjustable end weirs, part shields, splash deflectors and high solution flow manifolds.
Precious Metal All-Over Plating Cell
The All-Over Plating Cell is a primary component of Precision Process’ reel to reel plating equipment and is typically used to plate gold or silver over a base metal, such as nickel. The All-Over Plating Cell is a pass-through system combining a high, continuous flow of plating solution to the strip through a multiple sparger and overflow weir system. The system consists of a polypropylene or acrylic plating cell, anode frame with inert anode, and air wipe. An external solution reservoir with heater, filtration system and transfer pump provide fresh, high metal content plating solution to the strip material. The All-Over Plating Cell is designed for the continuous plating of strip material, pre-formed connectors, lead frames, and other formed or stamped components.
The All-Over Plating Cell is designed for the continuous plating of strip material, pre-formed connectors, lead frames, and other formed or stamped components.
Features include:
- High solution impingement to the strip through multiple sparger system
- Close proximity anode basket arrangement allows faster plating speed
- Adjustable side overflow weirs allow uniform solution flow
- Air wipe at the exit of the plating cell removes gross solution, reducing dragout
- Weir gate rollers at each end of the cell help guide the strip and minimize solution outflow
Equipment configuration options
Whether you require a single sided, double sided, "U" shaped, or a multi-strand reel to reel plating configuration, Precision Process can design, manufacture, and install your ideal system. Precision Process also provides pay-offs, accumulators, helper drives, programmable logic controllers, touch screens, and a variety of other options to meet your needs. See material handling and control systems for more information.
Download
Precision Process’s fact sheet on reel to reel electroplatingto learn more about the options available.